Water Feature Control Systems
Posted in Insights -
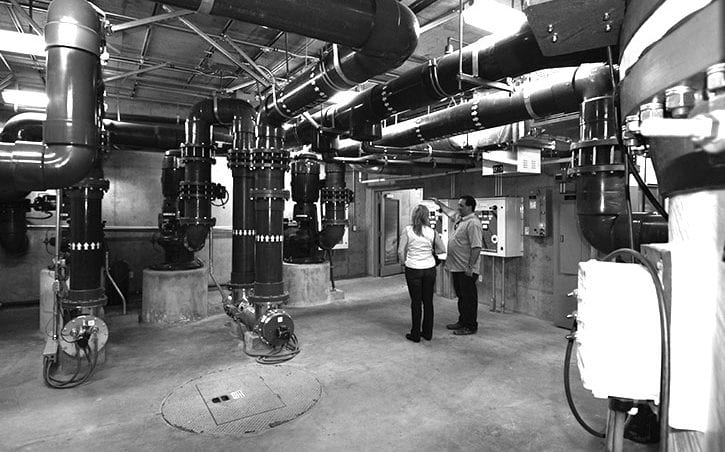
By Chris Roy, Director of Creative Design, OTL, Inc.
When people think of the control system for a water feature, often the first thing to come to mind is the electrical control panel – a grey box attached to some conduits, with knobs and buttons on the face, or perhaps a touchscreen. The reality, however, is that there are three control systems interacting with one another in any given fountain: the design of the fountain itself, the hydraulic system, and the electrical control system.
“
These systems run the gamut from extremely simple to highly complex; the level of the system’s complexity, generally, is reflective of the overall complexity (or lack thereof) of the fountain being controlled.
”
Design of the Water Feature
Not typically considered part of the control system, design elements of a fountain can, in fact, be very active control features. Examples include weirs (setting and/or maintaining water levels,) runnel design (slope, profile, and texture controlling flow rate and velocity), hydraulic head, nozzle selection, etc. Each of these components has an effect on the fountain’s water character, and these effects must be taken into consideration when the fountain is designed, lest they become undesirable controlling elements.
Here is an example of a design element functioning as a control element: imagine a dogbone-shaped water feature, with a broad waterfall pouring into a basin, which outflows into a narrow stream, which in turn flows into a pool and over another broad waterfall and basin before recirculating. This system could easily be built with a single pump recirculating water from the lowest basin to the uppermost pool above the first waterfall, replicating a system repeated countless times in nature. To function correctly, the complete system will have to be designed so that the flow rate through the stream equals the flow rates over the waterfalls; balanced flow rates are controlling the design/engineering of the water feature system. When the design intent is that the flows are not equal, the individual elements become active control factors.
Imagine an architectural water feature similar to the system described above. In this hypothetical system, imagine the two waterfalls are weirs with simple rectangular upper and lower pools; the lower pool of waterfall one is connected by a runnel to the upper pool of waterfall two. Let’s also imagine that each of the weirs is 20’ wide with a flow rate of 15GPM per foot of weir to create the desired water effect, and the runnel is 12” wide and 6” deep with 2” of freeboard. The weirs in this system have an as-designed flow rate of 300GPM; there are a huge number of variables in determining the flow rate through the runnel, particularly slope. Suffice it to say that, at a reasonable gravity-flow velocity, the runnel’s flow rate will be far less than the 300GPM required for the weirs. If this system were built as a simple single-pump system as described above, with a flow rate of 300GPM, the flow would quickly overcome the capacity of the runnel, and water would begin flooding out of weir one’s lower pool. Needless to say, water flooding out of the basin is certainly not within the design intent of the fountain and is going to make a lot of people very unhappy.
With this basic setup, the runnel is the restricting factor controlling the fountain; water flow must be reduced to the rate that the runnel will allow. The system can be made to operate without flooding – however, water flow over the weirs will be far below their intended flow rates. In this instance, the hydraulic requirements of the fountain’s elements are major controlling factors driving the engineering of the system.
While this hypothetical water feature can be engineered to run with a single pump (by incorporating large gravity drain lines hydraulically connecting the first weir’s lower pool to the second weir’s upper pool, creating a bypass route for the water not flowing through the runnel,) it isn’t an engineering decision the OTL team would recommend. The pipes will be large, the outflows may be quite conspicuous without careful detailing, and balancing the system to get the right flow through the runnel will be finicky; designing the system to be as “simple as possible” really doesn’t keep it simple at all, and doesn’t leave many options for control to fine-tune the aesthetics of the system.
The better engineering path is to design this as a three-pump system – one display pump for each of the weirs and a separate pump for flow through the runnel. Ideally, the third pump is the filter pump, with its discharge in the uppermost pool and suction in the lowest basin. In addition to flowing through the runnel, this pump contributes to the flow over the weirs, so that the size of the two weir display pumps (and associated plumbing) may be reduced.
This is just one example of how a water feature’s individual elements can be seen as controlling elements in and of themselves. This example can be extended across many aspects of a fountain’s design, from fountain layout through finish material selection.
Water Feature Hydraulic Controls
The next piece of the control system puzzle is hydraulics. Hydraulic control of the fountain has two aspects: passive (such as pipe sizing and water distribution) and active (valves). Passive control focuses on how water is routed through the fountain’s mechanical system. The goal of a water feature’s hydraulic design for the majority of projects is to create a balanced system with even flow. An example is supplying water to a manifold, which may be supplying fountain jets to a spray bar for a water wall. The manifold is typically supplied at two or more equidistant places to ensure even and consistent pressure and velocity in the manifold and in the display. Within a distribution system, pipe sizes may be reduced downstream of groups of risers to ensure consistent velocity and pressure throughout the system (similar to the design of an HVAC system’s ductwork).
Valves are the most typical active hydraulic controls and take a variety of forms. Most common valves (ball valves, butterfly valves, gate valves, needle valves) are manually actuated, though automated versions of each are used as well. A number of additional automated valves are used in water features, including solenoid valves, diaphragm valves, rate-of-flow-control valves, and others. These are typically actuated on commands sent from the fountain’s electronic control system, though some valves (such as rate-of-flow-control valves) are entirely independent and self-controlling, based on varying conditions in a feedback loop such as gradually opening to increase flow into a filtration system as the filter media gradually clogs between servicing.
Both manual and automated valves are used in two applications for water features: display/balancing and operations. Manual display valves are typically set during commissioning of the fountain to control flow to different areas of the water feature and/or to balance the heights of fountain jets, while operations valves are used periodically during operation of the fountain, such as closing off lines for servicing equipment, cleaning filters, and strainers, etc. Automated valves allow for a variety of changing display effects in a fountain, while automated operations valves allow for actions such as filter backwashing, sanitation chemical feed, and refill.
Water Feature Electrical Controls
The electrical control system is the brain of a fountain, and these systems can vary widely in complexity.
At the extremely simple end of the spectrum would be a basic, single-pump fountain system with a mechanical timer which turns the pump on in the morning and off at night. While limited in function, a basic system like this can take a variety of forms and quickly start gaining complexity – a line-voltage timer may actuate a high-voltage relay and motor starter for a large pump, for example, or the fountain may incorporate lighting, either on a separate timer, or configured with a photocell so that the lighting automatically comes on at night. The limitations of timers limit their use to all but the simplest of fountains; today’s high-tech water features require smart control capable of integrating multiple systems and feedback loops.
A programmable logic controller, or PLC, is truly the brain of most fountain systems. A PLC can be programmed to automate a variety of functions, such as turning the fountain on and off and offsetting start times for pump motors to reduce startup load on the system. Their real value, however, lies in the fact that they have both outputs and inputs. This is what allows them to function as a brain, programmed to perform a variety of actions based on a variety of inputs. Some examples are opening a solenoid valve to refill the fountain when low water is sensed, shutting off pump water if water levels drop too low, lowering the height of display jets (or shutting the fountain off entirely) based on input from a wind sensor, running simple programs for lighting, and running simple fountain choreography via variable frequency drives (VFDs) and automated valves. PLCs also are used in conjunction with more advanced show control systems, typically handling the primary functions of the fountain as well as activating the show controller, which handles the entertainment side of the fountain display.
While very simple fountains incorporating PLCs may still utilize basic push-button interfaces – On/Off or HOA (Hand-Off-Auto) – most also incorporate HMIs (Human-Machine Interfaces) in the form of touch screens, allowing users to operate equipment and view information through a series of menus. There are two PLC systems in widespread use: Allen Bradley and Siemens. While the implications of using one system or the other are of great importance to the panel builder and programmer, both systems function essentially identically as far as the end user is concerned. Pumps are typically controlled with variable frequency drives (VFDs) which alter their speed. This is a much more energy-efficient means of flow control than simply closing down a valve to reduce flow while the pump runs continuously at full speed.
Color-changing fountain lighting is controlled by a system called DMX, an industry standard protocol developed originally in the entertainment industry for theater and stage lighting. In more complex fountains, the control system architecture is designed so that the VFDs running the pumps are also controlled by DMX; this allows a master show control system to control all aspects of the fountain, lighting and water effects, cohesively. In fact, these show controllers are capable of controlling a variety of systems including audio, video, laser, and pyrotechnics. The controllers are typically modular and will be built out according to the requirements of a given project. On a musically-choreographed show fountain, for example, the control system will include audio controls including playback and I/O (input and output) for SMPTE and/or MIDI and will send audio output through a complete audio system including amplifiers and speakers.
There are a number of different show control systems in use, each with a different method of programming. Some are closely-held proprietary systems, while others are more openly available. While early show controllers required copious amounts of time dedicated to inputting lines of code and/or setting individual scenes on a large lighting control board, modern show controllers are completely digital and utilize advanced visual programming methods.
OTL uses a system called Syncronorm in all of our musically-choreographed show fountains, as well as many simpler fountains that still have choreographic capabilities. This system has a user-friendly timeline-based programming environment, and an efficient workflow for creating fountain shows, where a previsualization of the show is created from the same program that outputs the DMX protocol running the actual fountain show. Having the ability to go directly from previsualization to actual fountain show offers a huge time savings, which is very beneficial for project owners looking to add more shows to their fountains. The timeline-based interface also facilitates smooth transitions and choreography, allowing for graceful programming that enhances the correlation between water and music.
Summary
Water feature control systems are nearly as varied as fountains themselves, and control of a fountain is much more comprehensive than just the controls present on the electrical control panel. It starts with decisions made early in the design and engineering process of the fountain, and there are a number of different paths that can be taken at each step to reach a variety of outcomes. Experience with water feature design, engineering, construction, and programming are all key to creating a successful project. The fountain’s control systems bring all these elements together and ensure that the aesthetics of the project can be fine-tuned ensuring that the fountain creates the best possible experience for all to enjoy.
Chris Roy is the Director of Creative Design for Outside the Lines, Inc. In this role, he leads the company’s design efforts, working with developers, architects, and landscape architects, as well as engineers and vendors. Contact him at ChrisR@otl-inc.com.
Featured Articles
- Getting to Know OTL’s Administrative/Accounting Assistant Nathan Touche
- Centers With Well-Designed Experiential Water Features Can Attract 30,000 Visitors Per Week
- Fountains of Light: California Water Features Developer Opens North Texas Office
- AI and Facility Management: How to Avoid Potential Pitfalls
- Safety First and Last: Creating a Safe Site in any Environment